SHOWING TRUE COLORS : TARUM, THE NATURAL DYE FACTORY
I Made Arsana Yasa was born in Gianyar, Bali. He founded Tarum, the house of natural dye, in 2001. Back In 1995, he used to work using Japanese tinting techniques and synthetic dyes. However, with water pollution becoming a bigger and bigger concern for the local authorities, Made started thinking about obtaining sustainable, natural, non polluting dyes.
After experimenting with different possibilities for 3 years, he found the right technique for natural dyeing. Originally trained as an anthropologist, Made had studied people’s needs and habits at length. He had spent time in Rote island and was inspired by the local culture, which is how he came up with the project. He realised he needed to upgrade the dye quality, in order to reach international standards and be able to market his products both locally and worldwide.
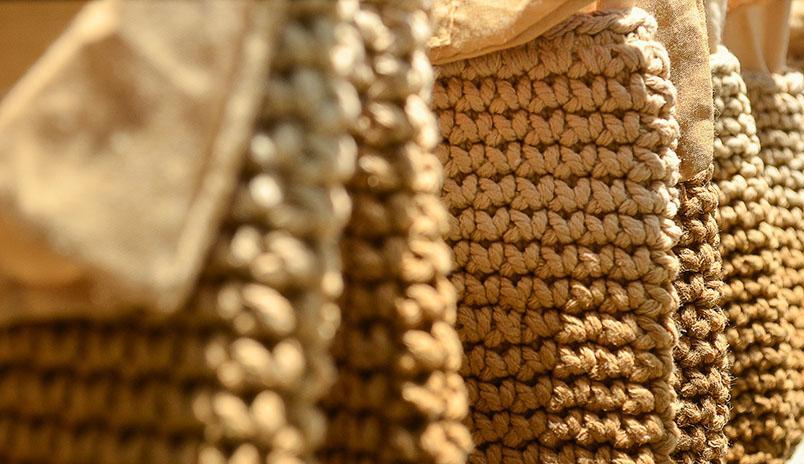
Tarum paved the way to a new approach, dying in an environmentally friendly, sustainable and holistic way, with a strong creative side, giving as much value to the dyeing process itself as to the natural raw materials that make the dye.
Thanks to Made, Tarum’s mission is to preserve and revitalise the traditional woven materials still used in fabric making. Several types of woven fabric are produced in the colour white, so that they may be colored and patterned. By developing this traditional weaving process, Tarum is now producing home decoration pieces such as bed throws, runner rugs, carpets, cushion covers, wall decorations and various other items like scarves, in an age-old and environmentally friendly way. These pieces are destined for export but also local businesses
INDIGO, THE MOST POPULAR COLOR but the hardest to extract
The first step in production is the creation of a color palette. The company has mastered the use of 5 plants (Mango leaves, Umbrella leaves, Mahogany leaves, Indigofera leaves, Sappan wood Bark), each one providing a “primary” color. The different combinations of these colors can create over 500 different tones.
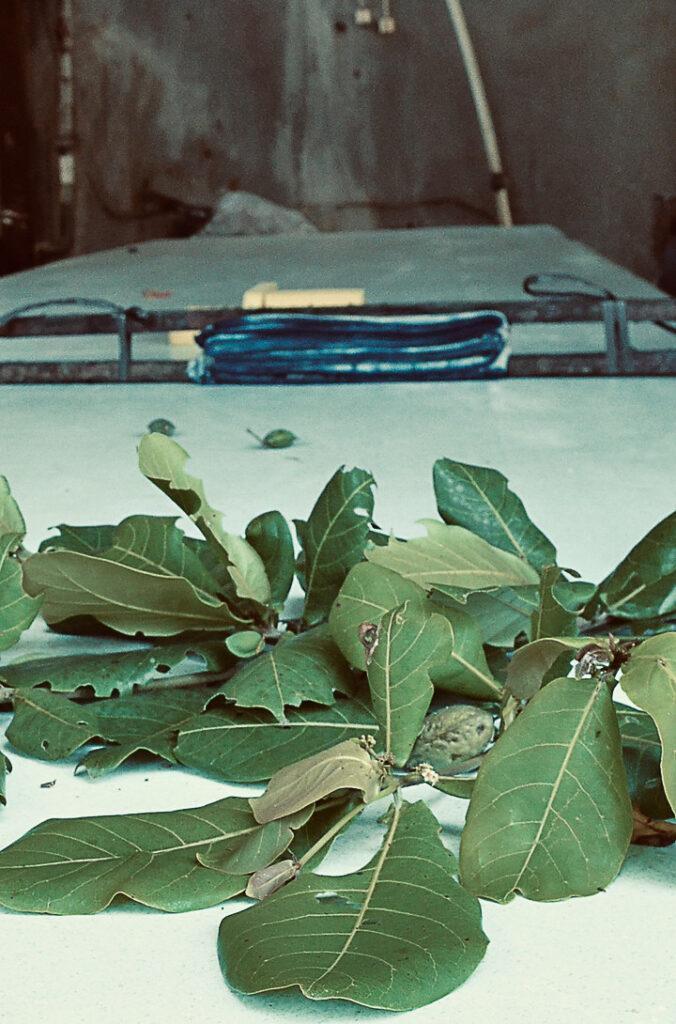
It all starts with the pigment or colour extraction. For 4 of these plants, leaves are boiled for 6 hours to extract the right color, but for Indigo, the blue tint can only be extracted by fermentation.
The fabric is soaked in warm water – 30 and 40◦C degrees- to open the fibers. The soaking lasts for 1 and 4 hours depending on the thickness of the fabric. This step is necessary to facilitate the dyeing process and for the color to bond to the fabric.
The dyeing session lasts between 10 and 15 minutes, depending on the desired color intensity. For light colors, 2 sessions are often enough, but it may take 5 sessions to obtain darker colors. The next step is to fix the colors. The fixation process uses limestone, vinegar and sea salt. Here again, the colors can be altered during fixing.
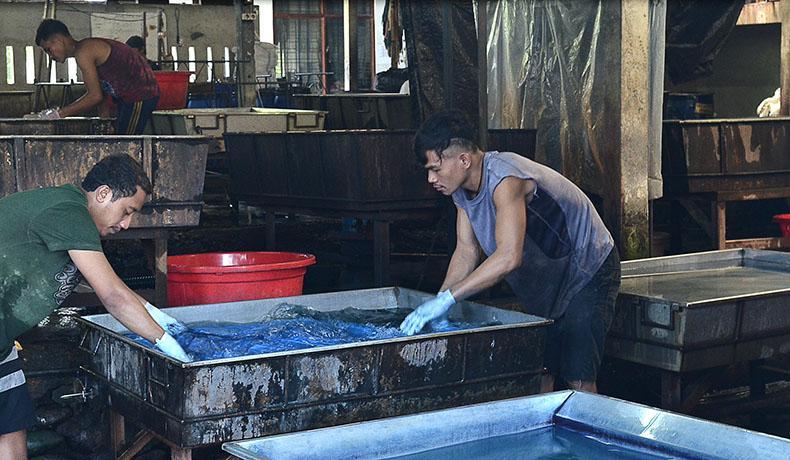
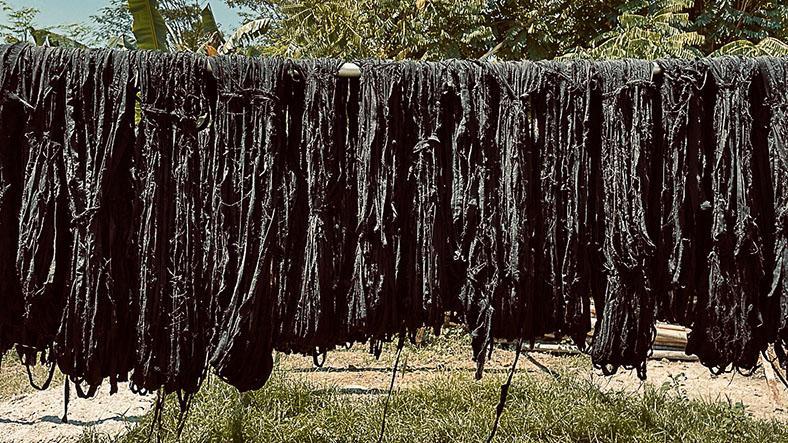
What is exceptional about Tarum is the use of organic dyes which have little impact on the environment and yet produce beautiful fabrics.
SUSTAINABILITY & EMPOWERMENT
Every individual creation is then made in the workshop. There is a station for patterns, one for yarn, and another for dyeing. Fabrics are processed here, sometimes from the customer’s own material. Leftover fabrics are used for re-dyeing.
Traditional methods are used in the workshop and most of the work is done manually. For instance, after drying, the yarn-or other thread- is woven by hand into large pieces (rugs…).
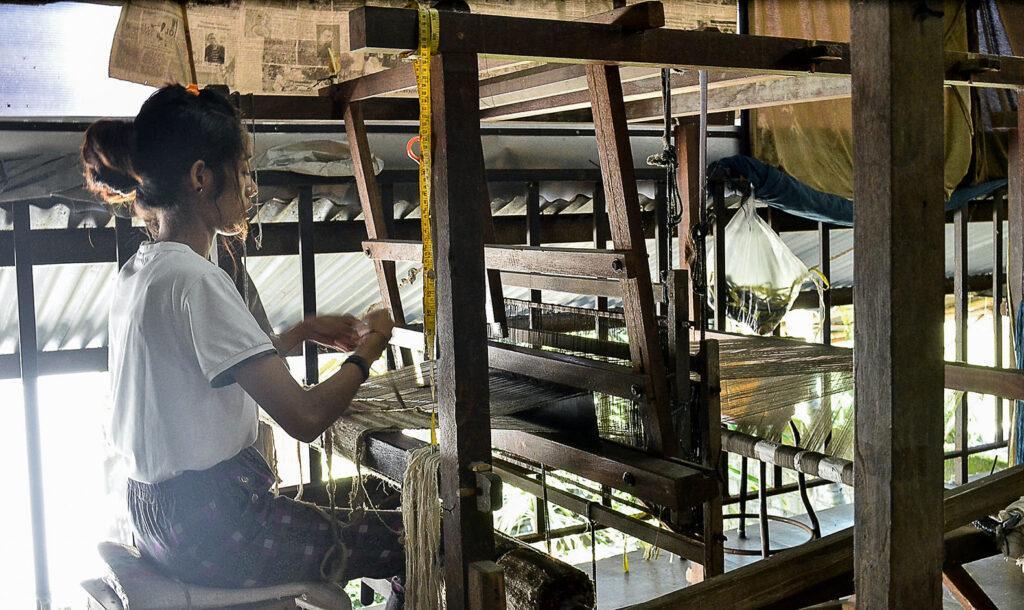
The dye procedure is what takes time. It matters little if there is 60 meters of 300 meters of fabric to dye. It will take a month with all the workers onboard. The more colourful the fabric, the longer the process. The weaving is the only process where you can sometimes save time.
The company has a plantation in Tampak Siring, which supplies the dying leaves and also offers a selection of T-shirts, clothes and linen using bamboo based fabric.
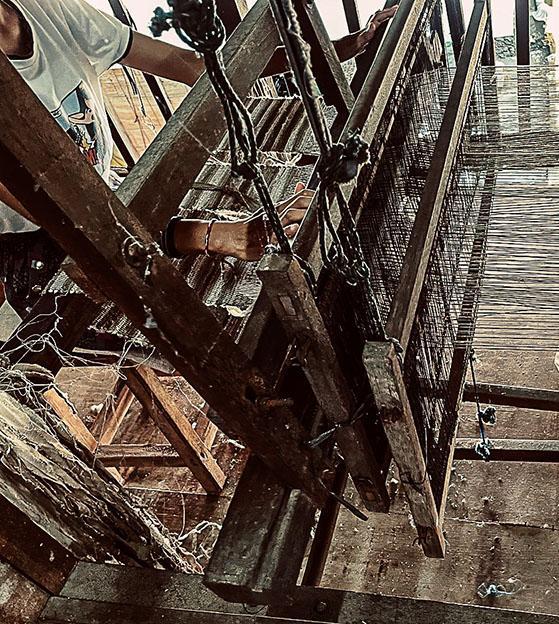
There are 4 TARUM factories in Indonesia (Two in Bali, including the main one, one in Lombok, and one in East Java), employing more than 100 people. The company is happy to hire people without qualifications and teach them the ropes, offering them the opportunity of a long term career.
LIFE AFTER COVID
Covid has had little impact on Tarum’s activity, with everything continuing almost entirely as normal, except for the shop, which is not open all the time at present. There still are a lot of loyal and returning customers who buy directly from there though. The plan is to start selling online soon, but obviously without the possibility of showcasing the raw fabrics.
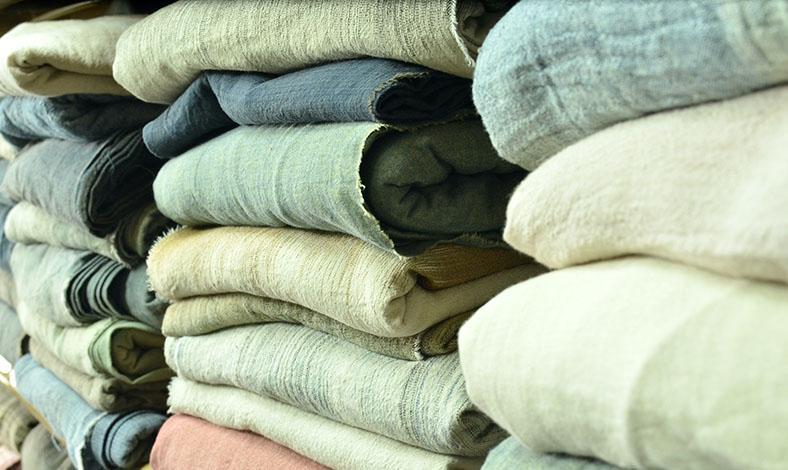
At the beginning of the lockdown, as order numbers dropped, the company suddenly had time and equipment available to work on new designs, creations and products, so much so in fact , that they gained 40 new clients by the end of 2020, and had to hire more staff to keep up with orders.
The factory is now offering workshop sessions that can be booked in advance. The idea for this popped up 10 years ago when a group of Japanese tourists visited the factory and were very curious to learn about the techniques. There can be up to 60 people attending the workshop.
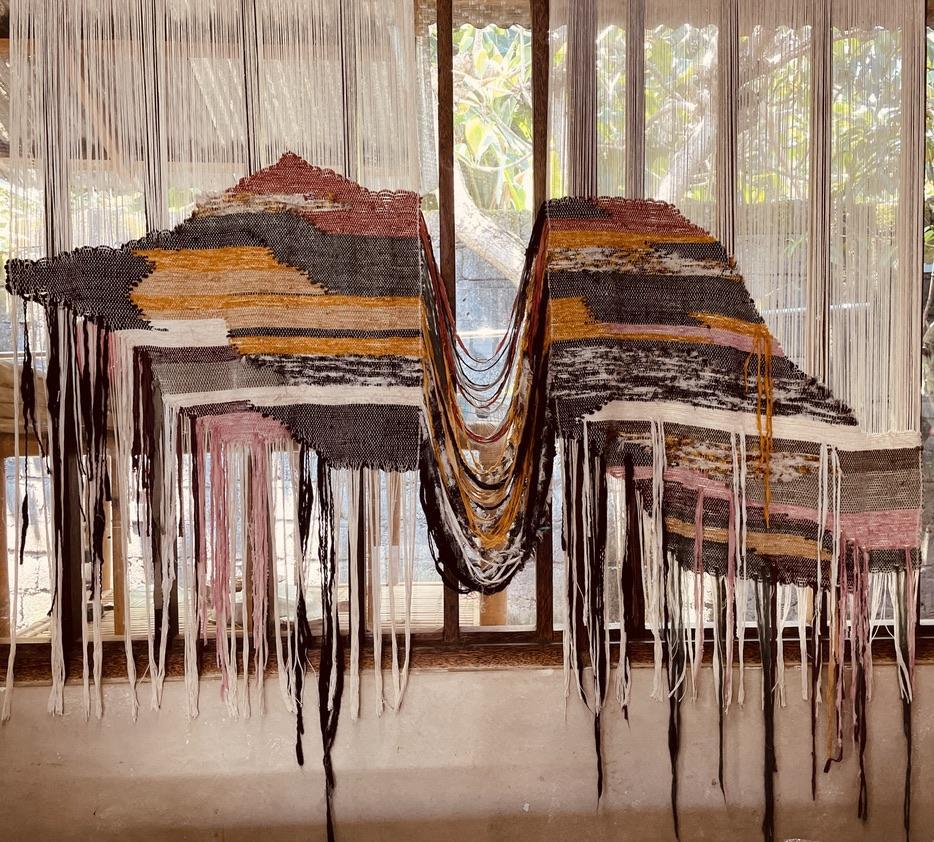
Tarum also works with hotels and resorts, which showcase the collections in their shops.
Tarum in numbers
Capacity : Dyeing : 2000 mtr /month
Batik/Tiedye : 2000 mtr/month
Interior : 5-10 carpet/rug, 250-300 pcs cushion/seater
Dipdye/Garment dye : 5000 pcs/month
Lighting fabric : 100 pcs lamp
Minimum Order : Dyeing; batik/tyedye 20 mtr
Handweaving width 50 cm – 100cm 70 mtr
Interior no minimum
Dipdye/garment dye 24 pcs
Lighting fabric /weaving 20 mtr
Credits : Cub Team