LAVA STONE DESIGN: FROM A FACTORY TO THE CREATION OF A DESIGN STUDIO
Edwige and Olivier are the French founders of Lava Stone Design. Based in Canggu, their company specialized in a noble and durable material: enameled lava stone. They create luxurious projects on demand and their expertise appeals to both professionals and individuals. They are the guardians of a unique know-how allowing them to meet very specific requirements. CUB went to meet them to discover this original product and find out how their Balinese adventure started.
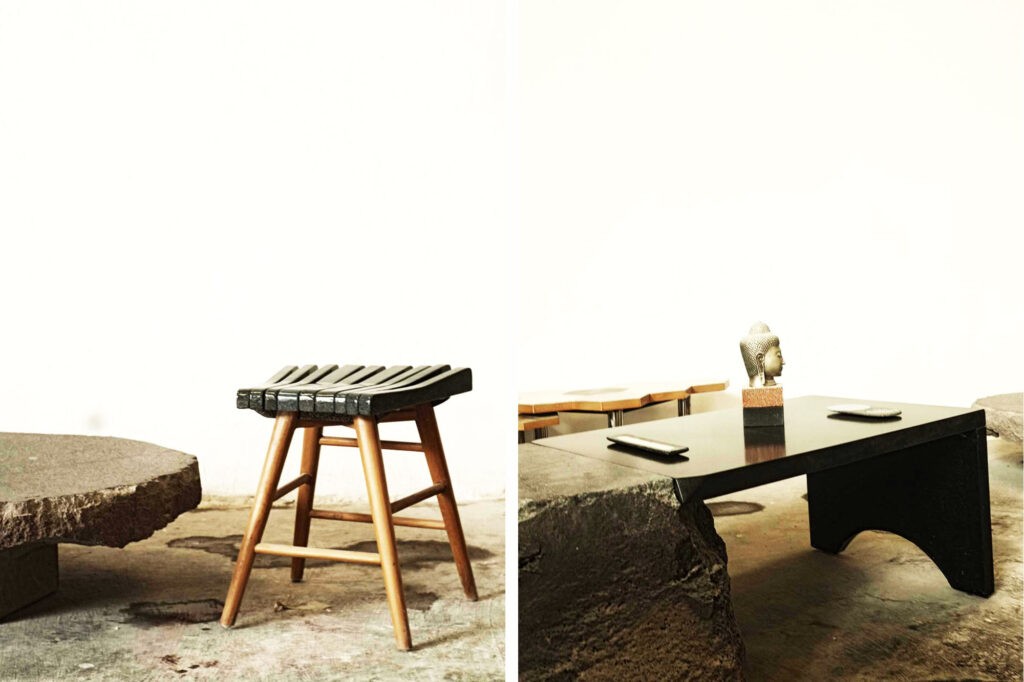
A JOURNEY FROM AFRICA TO ASIA
You were both previously expats in the Ivory Coast, where you spent 20 and 40 years respectively, can you explain how you arrived in Bali and developed this project? And the ups and downs of life as entrepreneurs…
Edwige: Olivier was running an industrial painting company in Abidjan but he fell in love with Bali during a holiday and wanted to be present on each of the two continents. To achieve this, Olivier recruited me. At that time, I was working in air and sea import/export. Unfortunately, following the violent coup d’état in Ivory Coast in 2012, the departure to Bali was postponed. Both of us found ourselves doing the same job. The situation was not viable, and after working for a company producing diaries for ministries (with integrated advertising), I decided to go back to France with our children to continue their studies. Bali came back to our minds, and we looked for different opportunities, at our arrival in 2018, and unfortunatltly we failed with a first partnership it was a stone business also.
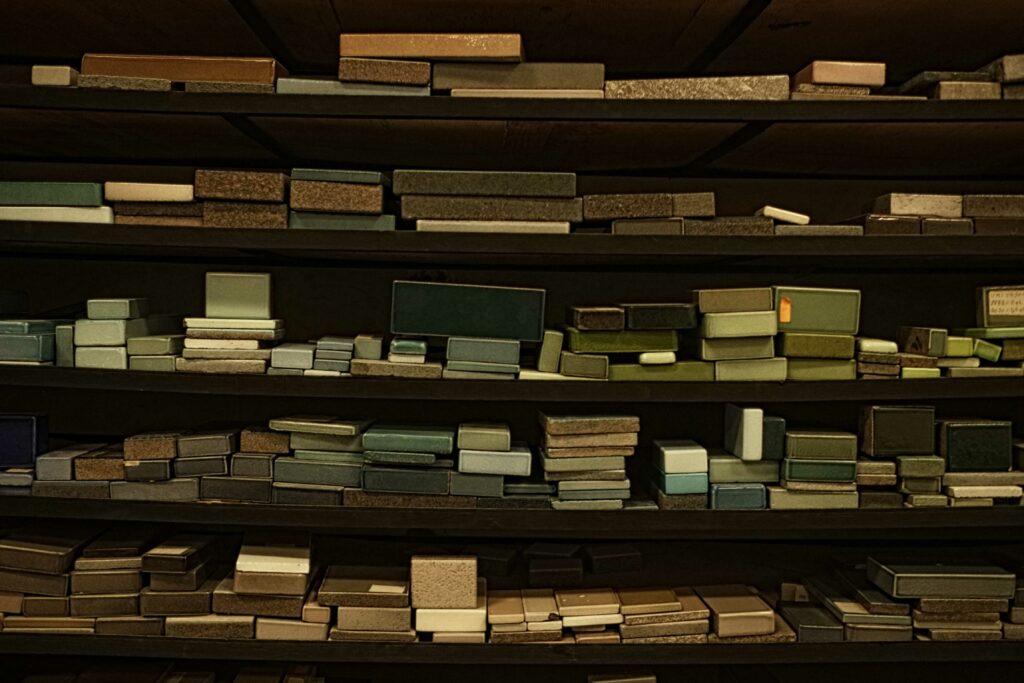
In 2019, we decided to set up our new structure, we were very quick to decide, caught up in the enthusiasm of the prospect of a new life and the idea of working with a new material. Yesterday, we were working with paint and stucco, now volcanic stone!
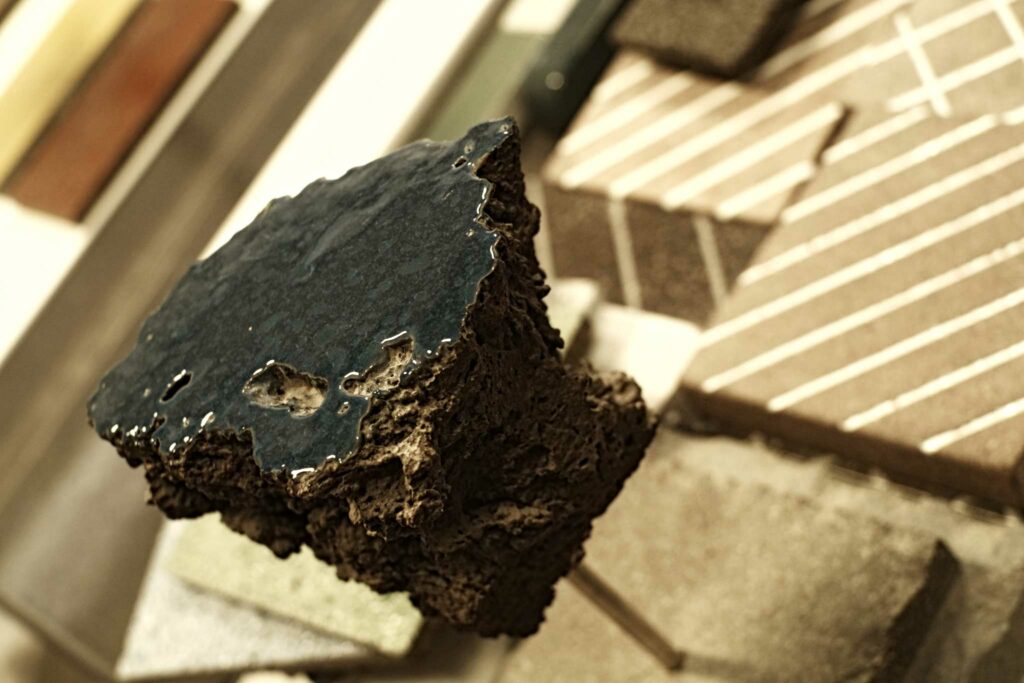
In 2019, we decided to set up a new structure. The Covid period allowed us to set up new processes and new products. It also allowed us to look for new markets, invest in a new oven, buy a lift and revamp the marketing, connecting with commercial outlets focused on Asia, the Middle East and Australia. We have been investing for 7 months now and plan to inaugurate a new showroom where our products will be well displayed. After an email campaign that didn’t work, I taught myself Instagram and got good returns. Today, we receive requests for very interesting projects every day via this social network.
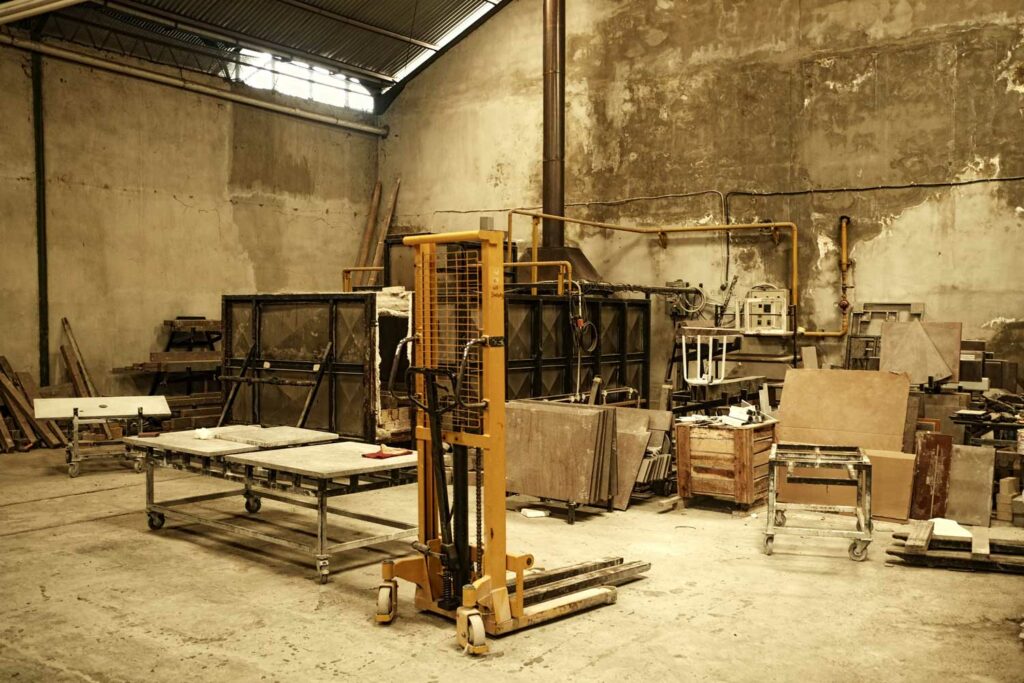

Big fans of positive thinking, we now have an order book filled 2 months in advance with 5 productions in progress and 10 orders in the pipeline with a visibility of 8 months. The stress has now changed sides, we now need to ensure that we can respond to all the orders and to a high standard!
Despite the difficult start, would you say that Covid has been beneficial to your business?
Edwige: Yes! It gave us time to take a step back and innovate! The great novelty is that we have gone from a product designed for flat surfaces (work surfaces, vanity tops, etc.) to objects with different volumes and new textures, in particular the Moon Effect.

This finish is more mineral and is an original, world-exclusive creation. Thanks to this new product, Lava Stone Design is starting to take market shares from our French and Italian competitors, and we recently won over a major project in Abu Dhabi.
THE TRANSMISSION OF INDONESIAN KNOW-HOW
Today, you, Edwige, are in charge of business development. Olivier is in charge of production. How did he learn about this new technical world?
Edwige: Indonesian lava stone is specific. Olivier learned on the job, acquiring knowledge from the existing team: when to open the kiln, what temperature, how to paint, what pigment to use. You have to be technical. This happened thanks, in particular, to Pak Kartika, one of the pillars of the workshop who really knows his stone. The process for painting stone is very different from making a painting where you fill in the blanks. The principle is to start with powder, the final colour of which is not known before baking. You cannot see what you are painting. If you use less pigment, you won’t see the result until it comes out of the kiln. Pak Kartika has a very precise and regular gesture. It is important to control the color because cracking is inherent to lava stone, it is like the enamel of a glass that cracks when baked.
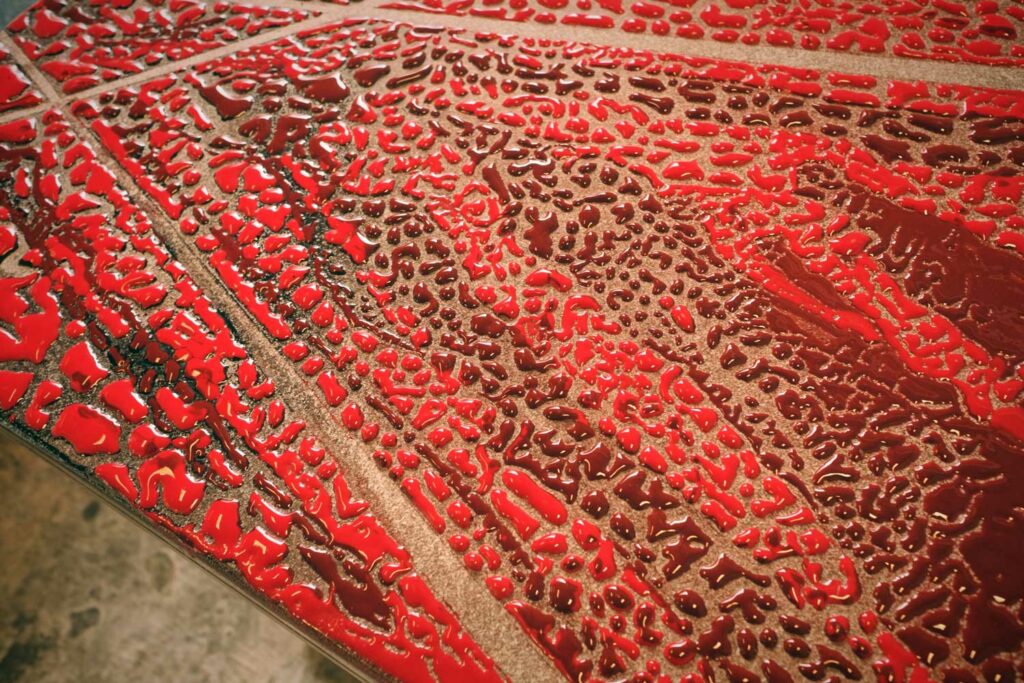
This is very interesting. Let’s talk about the technical possibilities then…
Olivier: We can make cornice angles, rounded angles, glue the stone… In the end, there are not many limits in terms of shape, except for the thickness. For example, you can’t make a 2 meters long table top that is 1 cm thick, the stone will break. There is a minimum thickness in relation to the length. Enamel and stone do not have the same heat resistance. Enamel is heated to 1000 degrees for 10/12 hours, sometimes 14 hours. Stone, on the other hand, is in a volcano, the blocks are thicker. In a kiln, it can twist as it’s cut. It is mineral, there is no control. So it’s a handmade product that is a little bit different every time.
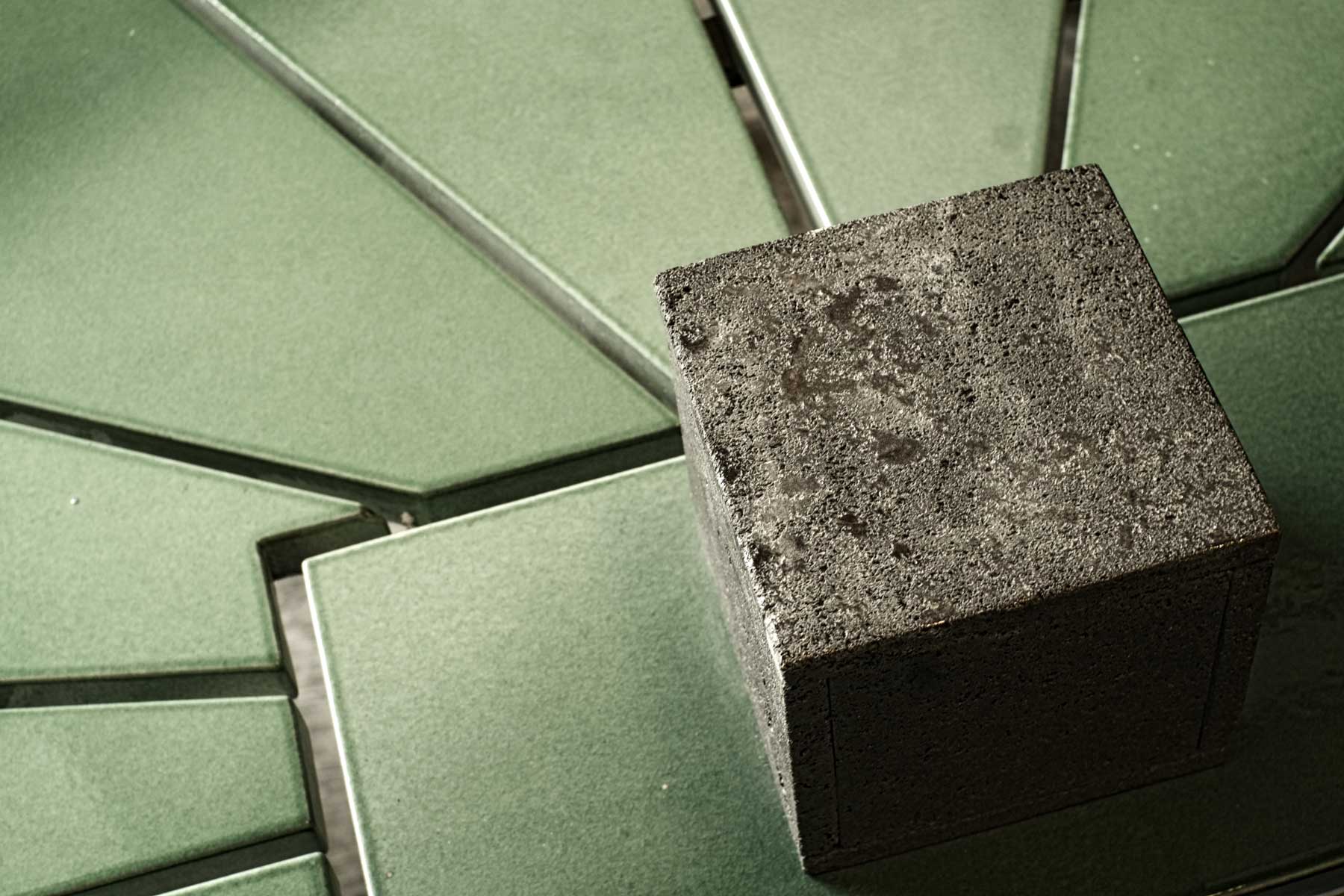
THE NATURAL EXTRACTION OF THE STONE
Regarding stone sourcing, Indonesia seems to be ahead of the game with an environmentally friendly method. Does this also apply to your stone?
Olivier: Yes, absolutely! Our lava stone comes from the open quarries on the Merapi volcano in Java, near Jogjakarta. No extraction is forced. The stone comes out of the volcano naturally, it rolls into the river or into a large plain. Unlike our competitors, we choose our stone, we do not attack the mountain and unlike marble, which is also quarried. We choose the stones ourselves according to the number of projects. A stone measures about 240 cm x 120 cm for example. These are stones that are tens of thousands of years old (millennial castings). The stone is removed with a winch and transported by truck to Bali. No prior testing of the quality of the stone is possible and it is always a surprise when it is cut. The size of the stone is always relative to the needs of the current project. Raw plate, Lava Stone Design then makes the shape. The size of the kiln determines the size of the standard plate and the bigger the plate, the more breakage. 60 cm / 80 cm / 120 cm is the standard plan size. So if you want a 400 cm table, then we can make several modules. Marble in comparison is max 250 cm. The most vulnerable step is during the firing to obtain the glazed color.
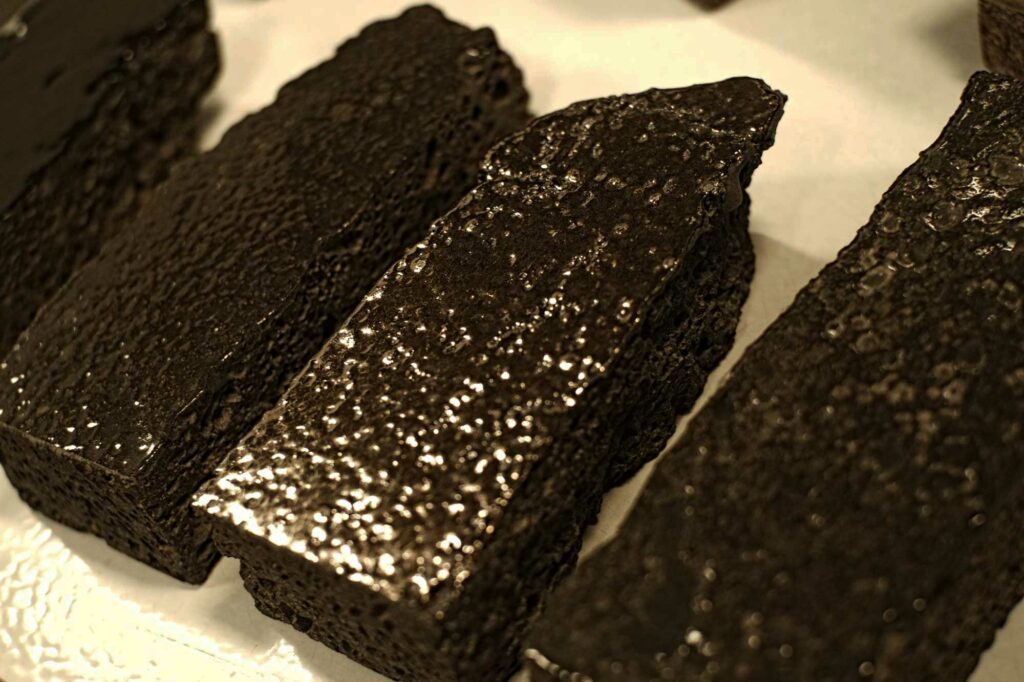
What makes your strength today is to be doing research on materials, like an creative studio…
Edwige: Since the Abu Dhabi project, more and more designers have come to Bali to discover what we really do and work directly with us. As a result, we are often asked about things that are a bit special. We don’t charge a fee for R&D, it really is a desire on our part to support interior architects and designers. They are familiar with Lava Stone because of the strength of the material and the huge range of colours. We manage to be competitive, about 30% cheaper than our competitors. What’s more, our location in Indonesia is also becoming an asset. With customers in Asia, HK or Singapore, for transport our location is also an advantage. We no longer work with Europe. The occasional conception with Stockholm (Sweden) because there are studios that develop projects in Asia. We have several future planned collaborations: IXO Design, United Stranger,Tom Fereday and Stellar Works (architectural firm well-known in the luxury hospitality business working). Here in Bali, we have a partnership with Piment Rouge, the lighting specialist, for whom we make lamp bases.
FROM A DESIGN STUDIO TO A REAL BRAND
Today, beyond your ability to meet demand, you mention you want to develop your own collections. Can you tell us more about this?
Edwige: Yes, absolutely. We have developed a collection of wall coverings tiles with the black lava stone with an unlimited range of colors. Our standard sizes are 40cm x 40 cm but the sizes are completely customizable. It is a product range that works very well for commercial counters or bars.
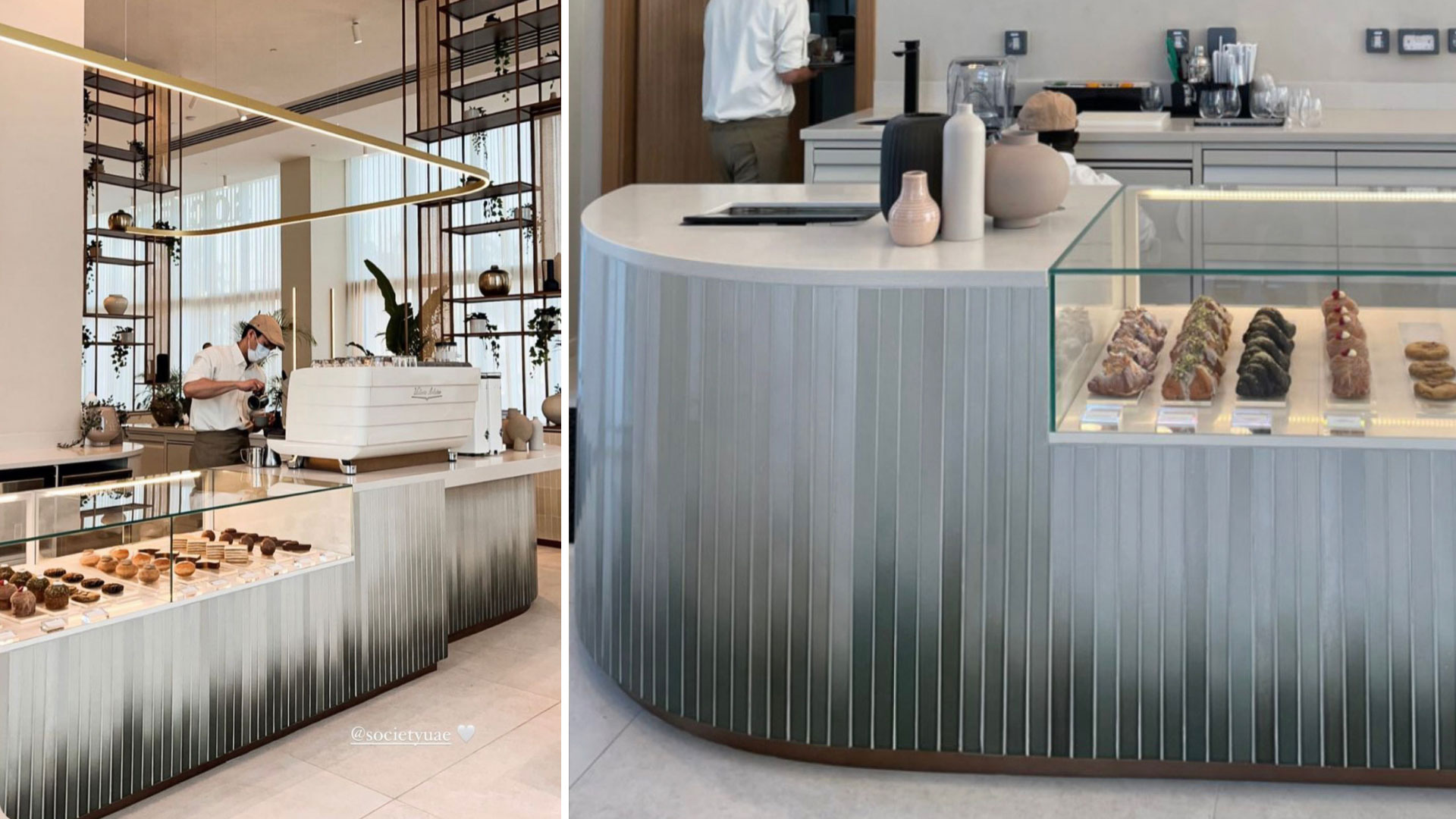
We have just completed a magnificent project in Abu Dhabi for a counter with tie and tie (radiant) slats. The radiant effect is Lava Stone Design creation.
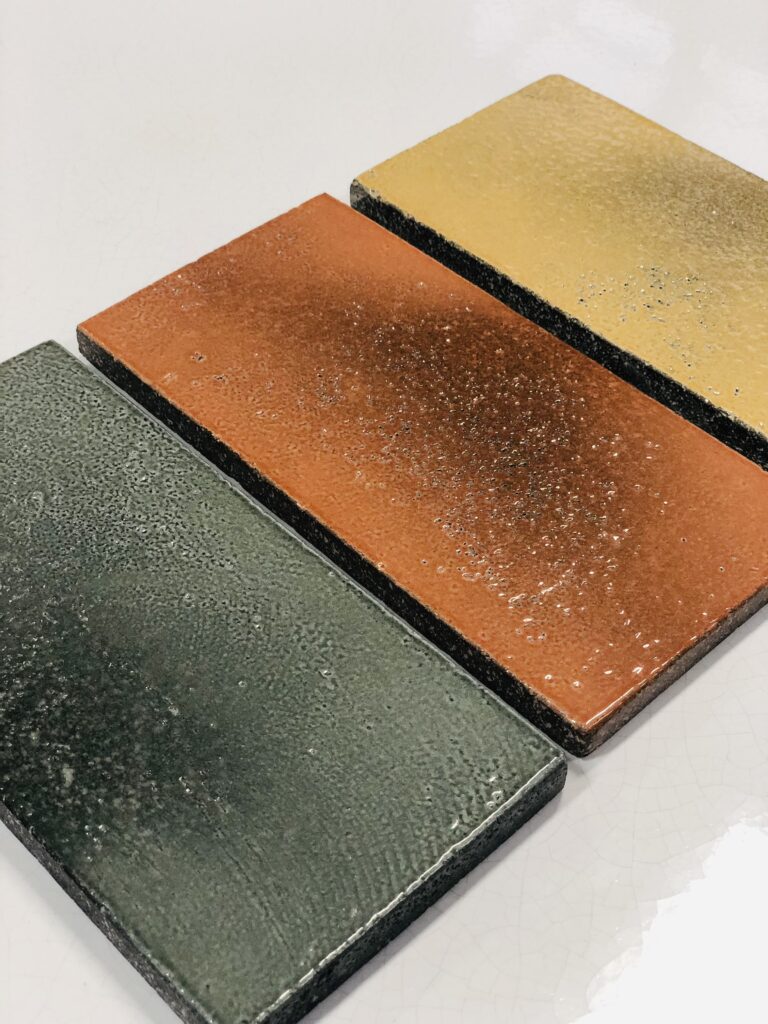
We developed “Mediator” tables in light blue radiant. It was a very interesting technical development because Pak Kartika is an amazing painter but not an artist! So it was a collaboration with Olivier, who used his experience with stucco in Africa to create the wave effect. When the tables came out of the kiln, it opened up new perspectives for us (price per Mediator table from 4 600 000 Idr).
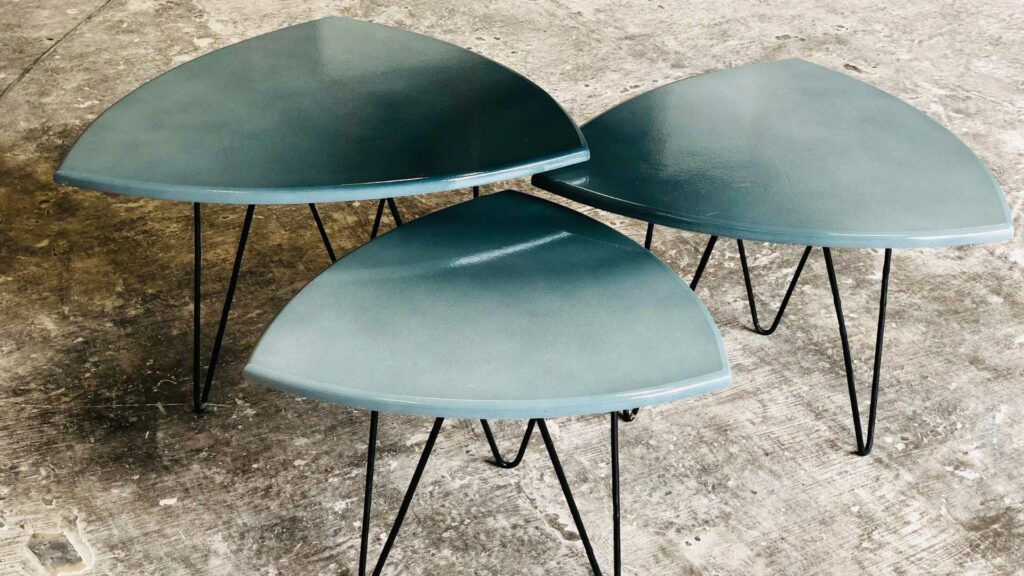
What do you dream about?
Edwige: Pragmatically, I’d say: stock more material to be even quicker in response, hire a technical director and an administrative manager… to take a break. That’s the price of success in a way!
Credits: Dex Bahya Noon
Editor: Julz Jenka